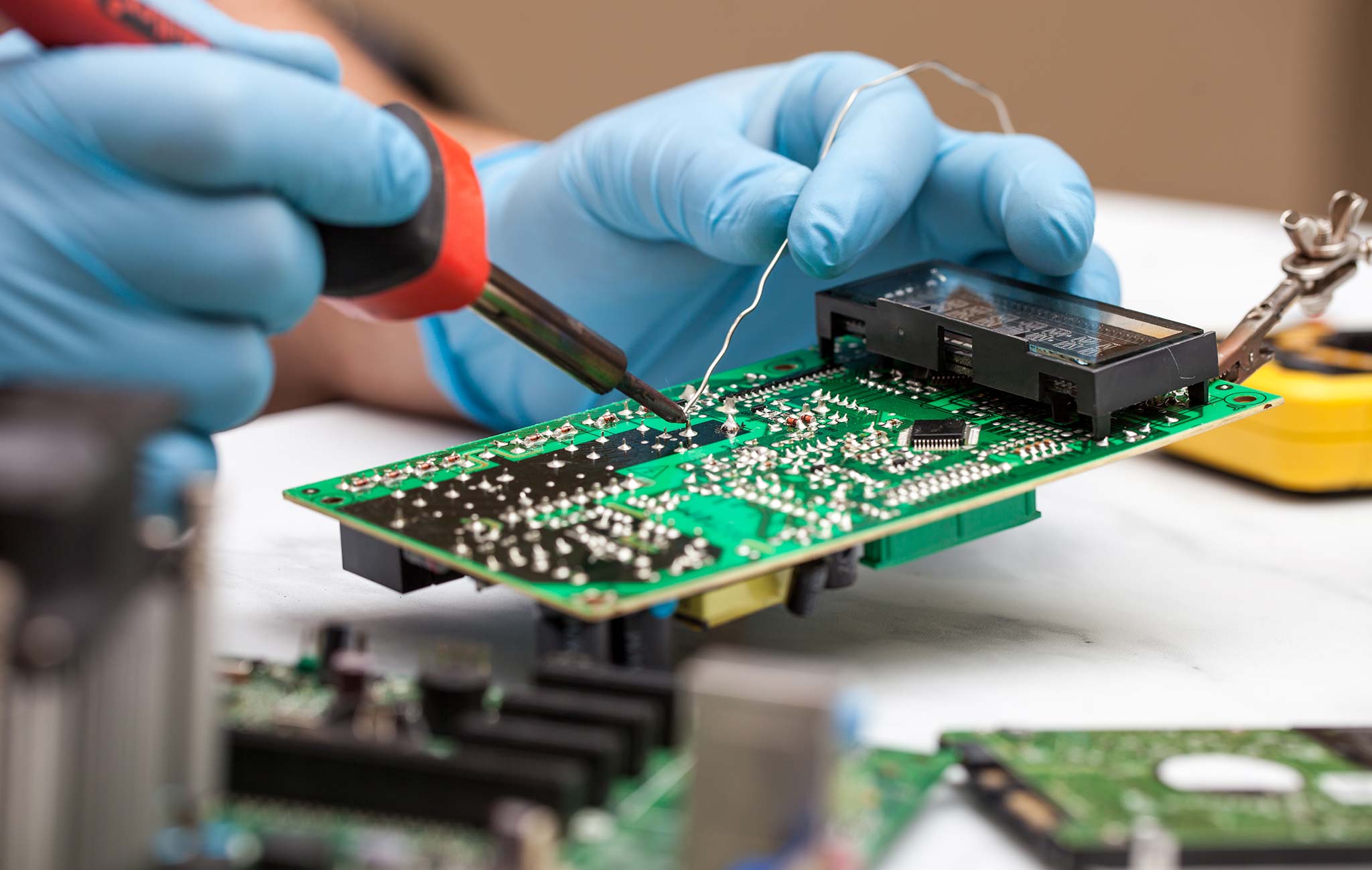
Soldering iron
Iron soldering and arc soldering do not expose the materials to be welded to a direct flame as opposed to flame soldering. Soldering iron is used for soldering and soldering very low melting point metals.
Principle of the soldering iron
The principle of soldering iron is the simplest since it involves heating a tip and putting this tip in contact with metal to cause it to melt. The soldering iron can reach up to around 400°C.
Description of the soldering iron
The soldering iron is a monobloc assembly including an electrical resistance embedded in the handle of the iron and transmitting its heat to an interchangeable tip. The soldering iron is basic and generally does not have temperature regulation like on the soldering station.
The energy of the soldering iron
The soldering iron is electric powered by the mains by a flexible cord. No temperature setting is provided as standard. When plugged in, it heats up as long as the resistance is supplied (from 370 ° to 420°C) it must be unplugged so that its temperature is lowered.
The soldering iron tip
The soldering tip is a kind of tip, one end of which is held against the heating resistance and the other end of which is cut according to the type of more or less fine work to be done. There are many shapes of tip, bevel, flat, single or double tips. Copper tips are found on entry level irons while better quality irons have solid electrolytic copper tips covered with iron, nickel and chrome.
Uses of the soldering iron
The soldering iron is mainly used for tin soldering (in fact soldering) of electronic components:
- lead solder,
- tin solder,
- the brazing with filler metal such as lead, tin optionally silver added.
The filler metal is tin with or without lead or silver which is distributed in the form of coils of tin wire of different diameters depending on the work to be done.
Soldering wire: continuous filler metal
Soldering requires the use of an electrode and sometimes a filler metal. Depending on the type of soldering, is used soldering electrode, the soldering wire or rods to be welded.
The main types of soldering wire
The role of the soldering wire consists on the one hand in providing the metal responsible for ensuring the connection between the two parts to be welded and in filling the joint to obtain a rigid assembly; and on the other hand, to ensure the passage of current by serving as a soldering electrode.
While it is often possible to fuse thin parts without the need for a filler rod, filler metal is essential for soldering thick parts.
There are two main categories in the soldering wire:
- the solid (or solid) wire which is simply a filler metal and an electrode
- the cored wire which is a filler metal, and an electrode plus a protective powder
The solid wire can be used without special precautions while the flux-cored solder wire can be either basic (B) or Rutile (R).
Characteristics
- The wire diameter is expressed in mm:
- Depending on the diameter of the wire, the intensity of the soldering current should be higher or lower.
- There are wires from 0.6mm to 3.2mm diameter (cored or solid).
- The composition of the wire according to the metal to be welded:
- Pure copper wire,
- Silicon wire,
- Manganese wire.
- The characteristic: solid wire or cored wire.
- G for solid wire.
- T for the cored wire
- The type of protective flux required according to the chemical nature of the substances constituting the fodder (cored wire only):
- Rutile fodder
- Basic fodder
- Need for gas
The utility of cored wire
In MAG soldering only (inert gas), protection of the soldering zone against ambient oxidation must be ensured either:
- With an inert shielding gas and a solid wire is then used;
- By the powder contained in the cored wire which evaporates in the flame to produce the inert gas and avoids vaporizing bottled gases on the weld area.
What to choose solid wire or cored wire?
The advantages of cored wire are:
- increase in productivity by increasing the deposition rate and by reducing handling (no gas cylinder),
- ease of use thanks to wide ranges of usable parameters
- increase in the appearance quality of welds
- the significant reduction of weld spatter and the improvement of the welder’s hygienic conditions by reducing the volume and the harmfulness of the fumes.